Dianor can offer a wide range of Diamond Dressing Tools
-
Wide range of Diamond Dressing Tools. Dianor AB manufactures and performs the service of high-quality Diamond and Solid carbide tools
-
Dianor AB manufactures and performs the service of high-quality Diamond and Solid Carbide Tools
Dressing Tools
Dressing Tools is a collective term for the tools used to shape and/or sharpening grinding wheels, mostly ceramic. To choose dressing tool means to choose technology for sharpening and dimensioning your grinding wheel and dressing parameters to achieve a desired result. The most important issues to consider are:
- Requirements on the grinded surface
- Tolerance requirements
- Straight – or profile sharpening
- Requirements for interval and time required for dressing operation
- Available machine equipment
- Grinding wheel properties i.e. diameter and width, grain size, hardness
- Series sizes
- Tool economy
We will help you find the right solution for your needs! Contact us
Different types of Diamond Dressing Tools
- Single point dresser natural or synthetic Diamond dressers. Consists of a natural diamond with one or more tips mounted in some sort of holder.
- Multi point dresser works with several diamonds in cut at the same time for better tool life or faster tightening.
- Synthetic Diamond in the form of square rods are used in both single-and multistone performance. These allow higher tolerances and smoother dressing results obtained.
- Diamond impregnated tool consists of a diamond powder bound in a sintered metal. Provides robust tools for tough applications.
Diamond qualities
- FE/GC Only one good tip. Natural diamonds are classified according to number of good tips and the amount of cracks and inclusions in the diamond. A perfect diamond is in the shape of an octahedron of six good tips and is free from cracks and inclusions. A high quality implies good heat-discharge capability which is essential for the life of the diamond.
- FC: Normal quality, at least four good tips. Limited inclusions.
- FB: At least five good tips, insignificant inclusions
- FA/OA: Diamonds of the highest quality. Oktaedrar with at least five good tips and virtually free from cracks and inclusions.
- TM: “Triangle maccles”. Diamonds of exceptional quality, shaped like plates with three tips
- LS: “Long Stones”. Diamonds of exceptional quality, shaped like elongated “grains of rice” with very constant cross-sectional area through the whole diamond.
We will help you find the right solution for your needs! Contact us
Synthetic Diamonds of two types exist in our dressing tools:
- Mono-crystalline diamond: “Monodress”. A rod with a square cross-section formed by a homogeneous synthetically produced diamantkristall. Like a natural diamond in a crystal lattice with certain special directions as to why it is important how the rod is twisted by the application against the grinding wheel.
- CVD-diamond, “Polydress”: As “Monodress” but Diamond’s structure is irregular.
Diamond Dressing Tools BVM/BVP
Blade-shaped with Synthetic diamond.
Dressing tools from the BVM series and BVP is used for profiling and sharpening of grinding wheels where high demands on precision and constant properties are set.
By synthetic, in the form of a rod, has exactly the same width and area throughout his lifetime, the grinding wheel structure is held constant and a high profile accuracy can be achieved.
BVM series and BVP has different types of diamonds. The BVM-tools consist of a “monocrystalline” diamond. Diamond, in these dressing tools are oriented correctly in the grinding direction. BVP-tools has a “poly-crystalline” diamond. Its random oriented diamond grains enables the diamond can be rotated freely. Even characteristics like hardness and price can determine the choice
In addition to this, there is a series of special design adapted to special applications. Contact us for recommendations.
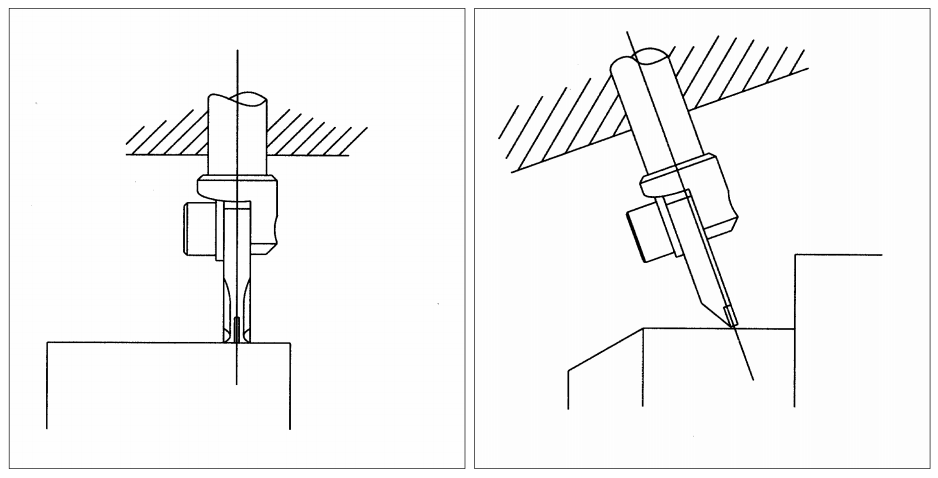
Dressing Tools BVM/BVP
Considerations for dressing operations with Diamond Dressing Tools
- Diamonds are sensitive to nature, shocks and overheating.
- The grinding wheel should be well balanced and free of vibrations and the tool well fastened.
- Tearing should occur in the same proportion as the slipoperationen.
- By tearing with coolant should the disc be flushed and be completely wet before the tearing, and the coolant is flowing continuously at tool engagement point. High flushing pressure is an advantage.
- When dry may not be tearing tool in surgery for more than a very short time. Let the tool cool down before the new procedures. Cooling not by adding coolant.
- Cutting depth normally 0.004-0.03 mm, max 0.05 mm.
- Feed speed 0.05-0.5 mm/Rev.